滚动轴承的疲劳失效与轴承钢中的非金属夹杂物的关系
王振华
(宝钢股份公司 设备部,上海 200941)
《宝钢技术》 2003年增刊
摘要:阐述了滚动轴承的运动机理、非金属夹杂物和材料表层疲劳剥离的相互关系,指出轴承钢中的非金属夹杂物是影响滚动轴承使用寿命的一个很重要的因素,提出提高钢的冶炼技术、改进冶炼设备、稳定工艺及拟定合理的检验标准和方法仍是降低轴承钢中非金属夹杂物含量的最有效的措施。
关键词:滚动轴承;夹杂物;寿命;疲劳剥离
1 前言
滚动轴承是一种应用十分广泛的机械零件,目前全世界轴承的销售额达300亿美元,中国占9%。轴承钢的产量达千万吨,中国占8%左右,已成为继日本、美国、瑞典、德国之后的第五个轴承和轴承钢的生产大国。但尽管如此,我国目前每年还需进口2 ~ 3亿套轴承(约2.5亿美元)及相当数量的轴承钢,用于关键设备及制造高品质的轴承,这不但反映了我国轴承和轴承钢的生产能力与先进工业国有差距,而且在轴承和轴承钢的产品质量上也同样存在一定的差距。就轴承产品质量而言,我国轴承钢的产品质量(主要指非金属夹杂物)的稳定性仍然是影响我国轴承产品质量(轴承的使用寿命)的重要因素。
2 滚动轴承的使用特性及对钢材的性能需求
2.1 滚动轴承的使用特性
滚动轴承是由滚动体(钢球、滚子和滚针)来承受系统载荷并传递机械运动(转动、摆动和直线运动)。在轴承内相对运动的滚动体和套圈滚道表面的接触处是处于高交变应力状态,一般而言,在点接触类型的滚动轴承内(如球轴承),钢球和套圈滚道表面的接触处的接触应力大约为2000 ~ 2500 N/mm2, 在线接触类型的滚动轴承内(如滚子轴承),滚子和套圈滚道表面的接触处的接触应力大约为1400 ~ 1800 N/mm2。
滚动轴承的一个非常重要的使用特性是:在上述的高交变接触应力作用下,轴承能在满足设备系统的要求(如:载荷、转速、振动、温度及精度等)的同时,持续运行所要求的时间或转数。这就是所谓的“滚动轴承的使用寿命”。
大量的轴承寿命试验数据证明,滚动轴承的疲劳寿命是相当离散的,而影响疲劳寿命离散性的主要因素之一是:轴承材质均质性及质量的稳定性。
2.2 滚动轴承对钢材的性能要求
鉴于滚动轴承使用的苛刻条件及特殊的抗磨、抗疲劳的要求,在20世纪开发了一类含1%左右的碳(C)和含1.5%左右的铬(Cr)为主的高碳铬合金钢,其主要特点是:可以采用现金的冶炼方法、技术和工艺得到很高的纯净度;经适当的热处理可获得具有均匀分布的粒状珠光体球化组织,切削加工性能良好;具有优良的淬透性和淬硬性,热处理后的显微组织和硬度比较均匀稳定;具有较高的接触疲劳强度和良好的耐磨性;经适当的热处理可获得很好的尺寸稳定性;并且具有一定的抗腐蚀性能;材料价格比较便宜。到目前为止,高碳铬合金钢仍是世界各国普遍用于制造滚动轴承零件的理想材料,其中GCr15和GCr15SiMn两个钢号使用最广泛,在我国这两个钢号的用量约占轴承钢总用量的80%以上。
历经半个多世纪,到目前为止尚无其他更好的材料取代高碳铬合金钢广泛地应用在滚动轴承制造业中。对高碳铬轴承钢的化学成分组成的认识,世界各国已趋于一致,几乎无大的变动。但人类仍在不断地探索提高滚动轴承使用寿命的途径,研究轴承材料的抗疲劳机理,并已充分地认识到钢材中的非金属夹杂物是影响滚动轴承使用寿命的重要因素。近年来,如何改进轴承钢的冶炼方法、技术和工艺,严格控制(检验标准、检测方法)轴承钢材中的非金属夹杂物的含量、尺寸大小、形状、分布和集聚,已成为冶金和机械行业共同关注和努力的目标。
3 滚动机理与滚动表面材料疲劳剥落
众所周知,金属材料在循环应力的作用下产生不可逆的结构变化,其特征是在这个区域内材料晶格滑移,进而萌生疲劳裂缝,而且试验也已证明:滚动轴承的滚动表层材料的晶格的滑移和疲劳剥落与滚动轴承的汉斯考特滑动、雷诺滑动有关[1]。汉斯考特滑动和雷诺滑动在滚动轴承运行中是不可避免的,汉斯考特滑动导致材料表层晶格滑移,实验证明在深沟球轴承的内套圈的滚动工作表面,在汉斯考特滑动区域内的强迫滑动运动产生了附加应力,从而导致这个区域内的材料表层的晶格滑移加重。在雷诺滑动区域内,表层金属材料中的非金属夹杂物的周围会收到拉伸和压缩的交变应力,这种交变应力使非金属夹杂物区域(也可称为一个空穴)的弹性能转变为变性能而产生裂缝,裂缝的两侧面反复受到挤压,裂缝沿主应力方向发展,最终导致材料的剥落。
4 滚动轴承材料疲劳剥落形式及与材料非金属夹杂物的关系
4.1 滚动轴承材料疲劳剥落的类型
滚动轴承材料疲劳剥落可分为材料的表面疲劳和表层疲劳两种。
(1) 材料的表面疲劳
材料表面疲劳的微裂缝起源于材料表面,随后由表向里,朝材料的表层延伸,最后裂缝又向材料表面扩展,形成材料的剥离。材料的表面疲劳不但与表面的形态、粗糙度有关,而且与润滑剂、润滑条件,特别是与外界异物的入侵及润滑剂清洁度等直接有关。
(2) 材料的表层疲劳
材料表层疲劳的微裂缝起源于材料表层,随后由里向外,朝材料的表面延伸和扩展,最后形成材料的剥离。材料的表层疲劳主要与材料表层的形态结构有关,特别与材料表层的非金属夹杂物的类型、尺寸大小、形状、分布和集聚状态有关。
4.2 滚动表层下材料的疲劳剥落与材料中非金属夹杂物的关系
滚动表层下材料的疲劳剥落可分为两个阶段:
(1) 表层下材料晶格的滑移
材料在循环交变的应力作用下,表层材料会发生不可逆的结构变化⸺晶格滑移,经不同的腐蚀方法后晶格滑移会呈现黑色区域(DEA)或呈现浅白色区域,即所谓的“白带”。“白带”与材料表面大约呈45°,并相互交错扩展。“白带”区域内材料局部强度和硬度下降,马氏体组织发生塑性变形,明显衰变。马氏体周围出现类似碳化物的区域,区域内颜色变化越明显说明马氏体晶格滑移越严重,晶格滑移的程度与滚动表面的载荷(应力)大小及载荷变换次数有关,晶格滑移是滚动表层下材料的疲劳剥落的第一阶段。
滚动轴承工作表层下材料的疲劳剥落的第一阶段占材料疲劳的极大部分的时间,所以控制滚动轴承的载荷、采用合理的润滑是延长轴承疲劳寿命的有效措施。
(2) 表层下非金属夹杂物处疲劳裂缝生成和发展
随着表层材料晶格滑移现象的出现和加剧,在表层材料下最大应力区域中的最薄弱处⸺一般是材料中非金属夹杂物处,会出现所谓的“蝶形”(见图1),碟身呈现黑色(非金属夹杂物的本体),而裂纹的二侧面因相互挤压而扩展(飞翼的形成),继而发生冷作硬化和塑性变形,并进行了新的淬火,所以飞翼呈白色,“蝶形”是沿最大剪切应力方向而产生的。显微金相分析又证实:微裂纹在“蝶形”的飞翼顶端萌生(见图2),在外界交变应力的继续作用下,微裂纹进一步扩展,最后导致材料剥落,这是滚动表层下材料疲劳剥落的第二阶段。
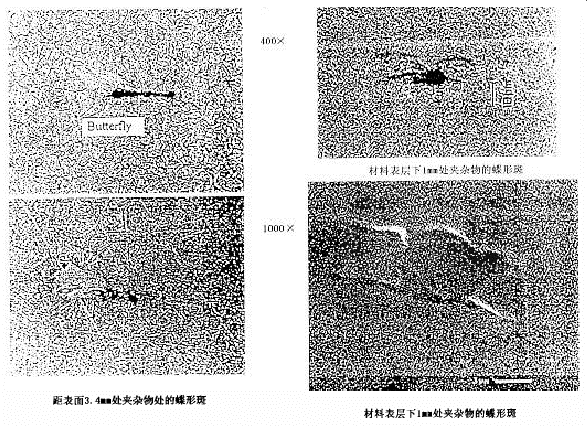
图1 表层材料下的“蝶形”
.png)
图2 “蝶形”的飞翼顶端出现微裂纹(1400X)
5 轴承钢中非金属夹杂物的检测和标准
钢中的非金属夹杂物如氧化物(Al2O3),硅酸盐(铝酸钙)等都具有脆性,其对交变应力非常敏感,塑性变形很小或根本不变形,容易在钢的基体组织之间产生间隔,破坏钢材的连续性。并在交变接触应力的作用下,在间隔处产生应力集中,形成疲劳源,直接破坏了钢材的连续性,是部分材料与基体材料分开或脱离。轴承钢中非金属夹杂物的存在形态多种多样,一般夹杂物含量越多,单颗粒越大,夹杂物离材料表面越近,其对材料疲劳寿命的影响也越大。因此非金属夹杂物对轴承钢的疲劳寿命是非常有害的。ISO已将轴承材料的纯度以A2系数列入滚动轴承的使用寿命计算公式之中。
2001年6月1日国家标准《高碳铬轴承钢》GB/T18254-2000正式开始实施,这是我国第一个有关真空脱气精炼轴承钢的正式国家标准,这不但标志着我国在轴承钢的冶炼技术和质量控制水平达到或接近国外的先进水平,而且对进一步提高我国轴承钢材料和轴承产品的质量有很大的促进作用。
6 国内外轴承钢的生产现状和产品质量
6.1 国外轴承钢的生产现状
20世纪80年代以来,世界上轴承钢的冶炼技术和生产设备有了很大的改进,轴承钢产量、质量也有较大幅度的提高。目前为止,无论从轴承钢的产量、质量,还是技术水平和钢材在世界市场的占有量,日本都在瑞典、德国、美国及前苏联的前面,处于领先的地位。
6.1.1 普通轴承铸钢
(1) 超高功率电弧炉(UHP)的推广使用
超高功率电弧炉具有改善热效率、降低电耗和提高生产率的优点,特别是炉外精炼技术的应用,电炉只要承担熔化、脱碳和脱磷的任务,这样超高功率电弧炉的高产、优质、低耗及高效率的优越性更加体现出来。目前电弧炉的容量已达150 t(Super – UHP)。
(2) 炉外精炼、真空脱气技术的不断提高
近年来真空脱气技术主要是循环脱气(RH)法,即将钢水在133.332 Pa(1 mm汞柱)的真空条件下脱去钢中的氢、氧、降低非金属夹杂物的含量。循环脱气(RH)法可有效地防止炉渣的卷入,钢中的含氧量可降低到8.2 × 10-4% ~ 15 × 10-4%。
炉外精炼(LF)是在钢包上加油加热、搅拌和脱气装置,在钢包内完成还原期,形成还原性炉渣,并进行脱氧、脱氢及脱硫等工序。如超高功率电弧炉(UHP)设备应用RH及LF技术,轴承钢中的含氧量可降低到3 × 10-4% ~ 10 × 10-4%。
(3) 电弧炉的偏心炉底出钢工艺(有倾炉装置)和钢坯的大型化
电弧炉的偏心炉底出钢工艺(有倾炉装置)的优点是:出钢时可留渣、钢流粗、出钢时间短,可增加钢流的紧密度,减少钢液二次氧化的机会,使钢材中的含氧量进一步下降(平均下降0.4 × 10-4%),可以改善钢中的非金属夹杂物的形态,使B类(氧化物)的细系列和D类(点状不变形夹杂物)粗系列的夹杂物得到明显的改善。
6.1.2 连铸技术的应用(IC)为:钢水(底铸法)⸺铸坯⸺钢材。
连铸轴承钢的工艺可以有效地减少钢材的再加热过程及热态时与空气接触的时间,避免了二次氧化,浇注温度低,如再进一步控制耐材的质量,轴承钢材的含氧量可以得到更号的控制。
分析表明:连铸轴承钢的含氧量在3 × 10-4% ~ 8 × 10-4%的范围内比普通轴承钢(IC钢)低2 × 10-4% ~ 3 × 10-4%,含氧量级别几乎达到真空电渣重熔钢的标准,但其成本却低于真空电渣重熔钢的成本。
试验表明:平均含氧量为5.7 × 10-4%的CC钢轴承的额定中值寿命为12 × 106 ~ 80 × 106转,而平均含氧量为8.3 × 10-4%的IC钢轴承的额定中值寿命为7 × 106 ~ 35 × 106转,CC钢轴承的额定中值寿命大约是IC钢轴承的额定中值寿命的两倍,这是因为CC钢含氧量降低的同时也有效的降低了对轴承寿命有较大影响的B类氧化物和D类点状不变形夹杂物的含量。
连铸轴承钢不足之处是:在压缩比较小和无电磁搅拌工艺时,钢材中会存在碳化物的偏析和芯部带状碳化物存在。
钢包、连铸坯、钢锭的大型化及大型加热设备的使用,保证了轴承钢材中碳化物的不均匀性,可以很好地控制钢材表面的脱碳层。
综上所述,目前国际上最先进的轴承钢冶炼生产工艺流程是:150 t Super – UHP电弧炉冶炼⸺偏心炉底出钢(EBT)⸺真空脱气精炼(LF + RH)⸺大断面连铸钢坯(或巨型铸锭)。
由于轴承钢冶炼设备、技术和工艺的发展,轴承钢中的含氧量及非金属夹杂物得到有效的控制,轴承钢质量有了很大改善,从而使轴承的使用寿命明显提高。
6.2 国内外轴承钢的质量差距
6.2.1 轴承钢的产品实物质量差距
目前我国年差近百万吨轴承钢中约50%~60%为真空脱气钢,RH及LF法的技术应用也比较熟练,其中上钢五厂、大冶钢厂生产的真空脱气轴承钢的含氧量绝大部分都在13 × 10-4%一下,其非金属夹杂物的含量也与国外先进水平相当。上钢五厂生产的轴承钢已被一些国外著名的轴承制造厂认可,并已在这些轴承厂在中国开办的独资或合资的轴承厂中应用。但总体而言,我国冶炼设备普遍较落后,工艺不稳定,产品质量波动较大,导致我国轴承产品使用寿命的离散性较大,与国外先进国家存在的差距主要体现在:连铸轴承钢材品种单一、规格偏小,仅为90mm以下的GCr15轴承钢,一些重要的轴承产品还要从国外进口,国内能制造的一些重要轴承还需从国外进口轴承钢材。
我国在1998年连铸轴承钢材制品批量投入市场,目前我国连铸轴承钢的年产量大约为15万t左右(以兴澄特种钢铁有限公司为主),连铸比达30%。
6.2.2 轴承钢的化学成分和非金属夹杂物的检验标准上的差距
新国家标准《高碳铬轴承钢》GB/T18254-2000是我国第一个有限真空脱气精炼轴承钢的正式国家标准。标准根据我国轴承钢的实际产品质量水平,并跟踪国际先进水平,对常用轴承钢的化学成分和非金属夹杂物的检验作了较严密和具体的规定。标准讲究实用性和先进性。但标准中轴承钢的化学成分和非金属夹杂物的检验标准与国外先进国家还有一定的差距。
(1) 标准是以轴承钢模铸的生产形式和实物质量水平为基础,不能全面反映连铸轴承钢的质量水平,而连铸轴承钢的生产成本低、纯净度高,是我国轴承钢生产发展的方向,因此标准应修正和补充。
(2) 轴承钢的发纹的检验
日本是轴承钢生产能力最大和质量最好的国家,其对轴承钢的品质检验有严格的要求,除对钢材的非金属夹杂物的含量控制外,还要对钢材进行由外到里的阶梯式的发纹检查(见表1)。发纹是一种存在于轴承钢材的表面或表层下细小裂纹状的缺陷,其形成的原因是钢锭表层中的皮下气泡或非金属夹杂物,经轧制变形后沿轧制方向呈单一或断续分布的细条状的缺陷。事实证明:轴承钢材中的发纹对轴承的产品质量(疲劳寿命)有一定的影响,发纹的检查和控制是对钢材中非金属夹杂物的另一种有效的检验方法。
表1 发纹数(JIG 4805 – 1990)
发纹长度,mm | 发纹数平均值(每一阶梯) |
>0.5 ~ 1.0 | ≤5.0 |
>1.0 ~ 2.0 | ≤1.0 |
>2.0 ~ 4.0 | ≤0.5 |
(3) 非金属夹杂物含量级别判定标准
我国目前对轴承钢的非金属夹杂物的含量的控制标准已达到国际的一般水平,但与一些先进国家相比还有一定的差距(见表2)。
表2 非金属夹杂物合格级别(不大于)
非金属夹杂物类型 | 细系 | 粗系 | ||
GB/T18254 | SKF(D33 B10001) | GB/T18254 | SKF (D33 B10001) | |
硫化物 | 2.5 | 2.0 | 1.5 | 1.5 |
氧化铝 | 2.0 | 1.5 | 1.0 | 0.5 |
硅酸盐 | 0.5 | 0 | 0.5 | 0 |
点状不变形夹杂物类 | 1.0 | 0.5 | 1.0 | 0.5 |
(4) 非金属夹杂物的检测方法
我国目前的检测方法主要是对10 mm × 20 mm的试样放大100倍,在视野内分别控制细系和粗系的单一类型的非金属夹杂物的累计总长度。事实上非金属夹杂物对钢材的疲劳寿命的影响不但取决于非金属夹杂物的种类的含量,而且与非金属夹杂物的尺寸、形状、集聚及分布有关,因此一些陷阱国家对非金属夹杂物的检测标准和方法也有所不同。
由于钢材中非金属夹杂物的分布和集聚是复杂的,没有任何评级图及标准能够代表所有不同种类和形状的夹杂物及其组合形式,目前我国已有了轴承钢材的非金属夹杂物的检验标准,但还应再吸取国外的先进经验,拟订检验细则(定义、判断和说明等),提高标准的可操作性,使标准更加实用,更有利轴承钢材和轴承产品质量的提高。
(5) 钢材化学成分的控制
我国GB/T18254-2000对轴承钢材中的金属Ti没有限制,而国外相关标准已对轴承钢的Ti含量有限制,如:NF A35 – 565 – 1994标准,SKF D33 B10001标准控制全淬硬轴承钢的Ti含量不大于30 × 10-4%。经对日本NSK和SKF的轴承进行测定,其Ti含量分别在10%和15%左右。轴承钢中的金属Ti以氮化钛形式存在,氮化钛比一般的氧化物更易偏析,在热加工时会发生破碎和弥散,当含Ti量高时钢材在加工过程中易出现疲劳、裂缝易扩散。
7 结语
滚动轴承在交变应力的条件下运行,不可避免地会因材料的疲劳而失效,而钢材中的非金属夹杂物是导致材料表层下疲劳剥落的直接因素,也是影响滚动轴承使用寿命的主要原因。提高轴承钢的纯净度,采用先进的冶炼设备和技术,稳定工艺,严格执行现行的有关标准,扩大真空脱气精炼轴承钢的生产能力,提高轴承钢的连铸比,降低钢材中的非金属夹杂物是延长滚动轴承使用寿命的一个重要措施。
参考文献
1 王振华. 实用轴承手册. 上海:上海科学技术文献出版社,1996:8.
编辑:任燕
(改稿日期:2003-05-16)