我国钢球制造技术现状与展望(三)
中国钢球工业的现状和问题
3 中国钢球工业的现状和问题
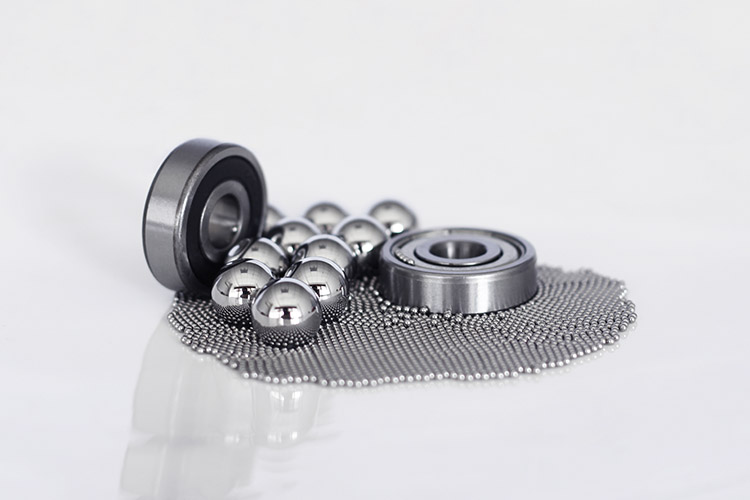
高精度轴承钢球
中国钢球工业自1948年生产出第一批产品已有56年的历史,从技术进步和行业发展看,改革开放后的发展是最快的阶段,目前我国钢球行业已经能生产0.5~200多mm的钢球,材料以GCr15为主,还大量生产低碳、防磁、防腐蚀、耐高温、有色金属、各种陶瓷和非金属材料球,精度已经能批量生产G1000~G5,产品广泛用于轴承、工程机械、家用电器、汽车、农业机械、机床、摩托车、冶金、化工、仪器仪表……,全国钢球生产点不少于几百个,其中有上千人的大企业,也有几个人的小工厂,有从毛坯到成品独立加工的,也有只加工某一工序的,形成了一个大企业周围分布无数个小企业和生产点的大局面,这种局面加快了钢球行业的发展,但也出现了无序的竞争,这种竞争不仅在国内,而且超越了国界,中国已经成为世界上钢球企业最多的国家,也是产量最大的国家,但要成为钢球生产强国还有很多问题需要解决。下面就中国钢球行业的现状和问题作一分析。
3.1原材料方面
制作钢球的钢材有很多品种,但实际能供应的品种甚少,有些虽能生产,但量少的无法提供。碳钢球用的是建筑用材,没有理想的低碳钢球用材。轴承钢的标准从两部协议已发展到GB/T18254-2000,GB/T18254-2001标准,中国终于有了轴承钢国家标准,通过引进、改进、更新设备,产品质量有了很大的提高,国际上的跨国轴承公司、汽车配件公司已经可以采用或正在对国内钢材进行认可,上钢五厂是他们的首选目标,经过加价优选的材料无论是氧含量、钛含量、夹杂物上都有提高,为优质钢球的生产创造了条件,但价格要高于一般产品。从总体上说,我国轴承质量稳定性较差,波动大,当市场供大于求时,质量往往会好于供不应求时期。一些信誉度差的钢厂以次充好,为提高成材率,减少头部切除长度,或者将被切除部分不该用于钢球的,因管理不善,混入了钢球用材,造成钢球质量后患无穷。钢材的裂纹仍是钢球行业头痛的事,加工前局部裂纹很难发现,成球后钢厂不认帐,这样增加了钢球行业的质量风险和成本。另外,因轴承出现无序竞争,相互压价,低价竞争,带来了钢球的无序竞争,低价竞争,而钢球又是形状简单大批量生产的机械零件,材料在产品成本上占最大的一块,钢材的价格和质量对钢球影响很大,钢球用材,由于它是全工作面产品,比轴承要求更高,按传统的要求,用于钢球的钢材只能用模铸工艺生产的,钢锭的头部不能用于钢球。由于受价格因素的驱动,市场上各种劣质钢材时有出现,个别企业用国产连铸钢材和低价劣质钢材大胆地用于钢球,这样造成了市场的混乱,质量的混乱,这必须引起有关方面重视,使中国钢球行业沿着公开、公正、诚信、有序竞争和健康的方向发展。
3.2 工艺方面
由于改革开放加强了国内企业与国外企业的交往,滚动体专委会经常组织有关企业研讨、交流、攻关、考察,使国内钢球企业较多地了解到国外情况,促使国内钢球工艺逐步优化,从总体工艺流程来看与国外大同小异。总加工留量上,由于受机床、材料、模具的限制要普遍大于国外。在工艺的实施细节上,或称专用技术上各家企业百花齐放,总体上还有不小差距,规范性太差,研究深度还不够。
3.3 辅助材料方面
改革开放以来是钢球行业发展最兴旺的时期,也带动了相关企业的蓬勃发展。
砂轮是磨削钢球的重要工具,原来仅依靠一砂、二砂,质量问题长期得不到解决,无论是耐用度、外观和外形尺寸几十年一贯制,引入了竞争机制,几十年得不到解决的问题,基本得到解决。80年代初引入我国的2000#树脂砂轮现已实现国产化,但在使用效果上与进口尚有一定差距,4000#树脂砂轮的攻关工作还在进行中,目前4000#以上的树脂砂轮尚需进口。
磨板的质量直接影响钢球的表面质量,经过多次攻关取得一定成效,但由于铸造行业变化较大,人员变更也大,技术力量分散,质量稳定性仍较差,与国外还是有不小的差距,尤其是精磨板的质量不稳定直接会导致钢球表面质量的不稳定。
水溶性、油溶性磨削液是精研和精磨钢球的重要原料,它们是多种化工原料调和而成,由于我国化工原料品种少、质量波动大,导致磨削效果差异大,最终影响钢球表面质量的稳定性。目前部分企业还是依靠进口原料,这样成本也会相对提高不少。
光磨板是锉削球坯用的合金铸铁板,自70年代开发成功至今,生产厂一换再换,专业人员缺乏,产品能用,但缺少进一步改进提高的能力,与国外相比有不小的差距,具体表现在磨削效率、耐用度、砂眼等问题,它直接影响钢球的质量和经济效益。
各种磨料是钢球生产所必须的辅料,传统的精研钢球用的磨料是三氧化二铬,它在我国是一种化学试剂或工业纯,它的技术指标是化学成分纯度的百分比,作为磨料需要的是硬度、粒度、颗粒均匀性、杂质含量和抛光性能等指标,因此使用与生产出现明显脱节。在国外,同样是三氧化二铬,不同的用途有不同的技术指标,这样适应性就强。
从以上的砂轮、磨板、磨削液、磨料现状分析,总体上有很大进步,为我国钢球技术的发展作出了贡献,但离国际先进水平及用户要求还有很大差距,愿他们继续为中国钢球赶上国际先进水平作出努力。
3.4 企业管理方面
任何一个企业真正要上水平,一定要具备两方面条件:一方面要有严格规范的管理,另一方面要有先进的技术,二者缺一不可。对钢球生产来说更是如此,钢球看是简单,真正做好真不容易!有好的技术能生产出一批或几批好球,要有稳定的质量,没有有效的管理,稳定便成为空话。
改革开放后不但引进了不少钢球设备、测试仪器,也引进了一些先进理念,甚至一些好的管理方法,好的理念逐步被我们所接受。随着质量管理体系的广泛推行,和日常暴露出的一些问题,管理的重要性越来越明显。我国主要的钢球企业,最早的五大厂全是国有企业,后来发展到十大厂甚至更多,基本也主要是国有企业和少量集体企业,因此这些企业在书面管理上做得比较到位,实际操作上尚有不足。特别是一些先进的、全新的管理方法推行难度较大。随着经济改革的深入,国有企业和集体企业正逐步向股份制方向转换,管理也正逐步去满足这种转换。90年代产生的钢球企业主要是民营企业,从企业数量上远远超过前40年,但总体生产能力仍是前40年的企业占主导地位,这些民营企业起步时往往是家属式的,企业发展了,家属管理模式适应不了生产的需要,原有的管理模式向高一级形式变化。因此这一类企业的管理只是初级阶段的管理。总之,国内钢球企业的管理与国外先进企业相比差距更大,这一方面是因为我们的企业进入市场经济时间不长,企业如何适应市场经济,摸索适应我国国情的有效管理需要时间,国外一些好的经验应该借鉴,但也不能全搬,因为无论是人员素质、企业规模、产品结构、硬件条件、设备状况、生产组织形式均不相同,要把国外的经验与国内实际情况结合起来,才是最有效的。另一方面,钢球的低价竞争客观上也影响到企业在管理上的投入。
3.5 技术标准问题
钢球的国家标准第一次制定并推行是在1964年,第二次修订的版本是1977年,第三次修订是1984年,这三个版本都是原则上部分采用ISO标准,由于当时的工艺水平低,常规生产无法达到国际标准,按当时的国情,某些项目在ISO标准基础上作一调整,制定了自己的标准。随着钢球技术的发展和工艺水平的提高,原来执行的国标已落后于实际水平,由此制定了新的国家标准,即GB308-89标准,为向国际水平靠拢,新的标准等同采用ISO3290-1975,除了没有采用英制规格外,其他已与国际接轨,ISO标准的采用,与国际交往有了共同语言。1998年,国际标准化组织又颁发了新的钢球标准,为赶上先进水平,我国等同采用了此标准,颁布了GB308-2002标准,新标准引入了表面不平度和形状参数的概念,给出了波纹度的定义,对表面粗糙度定义作一修正,优化了球的尺寸,增加了G24、G60,Ra的数值有所压缩,这样真正与国际标准同步了,更有利于中国钢球发展,并与世界融为一体。
3.6质量现状
中国钢球从材料上分,主要有三大类:一类是低碳钢,这类材料的产品档次较低,由于价格原因,原来向日本、台湾等地采购的都转入中国大陆,也有一些境外企业转移至大陆生产。由于这类产品使用要求低,虽有质量标准,而价格标准更为突出,材料问题、热处理渗碳问题、压碎值问题,混球和缺陷球比例过高也许被称为垃圾球的主要原因。第二类是不锈钢球,其中有马氏体不锈钢和奥氏体不锈钢,马氏体不锈钢球要求要高于奥氏体不锈钢球,但总体要求会低于轴承钢,因此质量矛盾也不突出。第三类是轴承钢钢球,这类材料在钢球中占主导地位,在这类钢球中10mm以下的数量最多,因此,中国钢球的技术进步、引进技术的消化、工艺改进、先进技术的采用推广、总的物力财力的投入在这方面也是最大的。在原机械部组织下,通过“七五”科技攻关和大循环水剂精研技术的推广,使中国钢球进了很大一步,目前国内广泛采用的就是此成果的基本内容,只要按一定的规范进行操作,此工艺获得的钢球球形误差、球直径变动量、表面粗糙度Ra都能得到满意的效果,基本能达到国外同等水平,甚至更好,但Ry的数值往往不太理想。在批直径变动量上,工艺技术上不存在问题,要达到标准也无大碍,但操作和调整不当,个别数值会偏大,与国外实物质量比会出现一些小问题。尺寸定值上,国内问题较大,同样的钢球各家测值结论不一,这与测量方法、仪器、环境、人的因素都有关。钢球的压碎值一般都能达到标准(JB/T1225-2001),但与日本相比均会偏小。钢球的动态性能,是低噪音轴承对钢球的重点要求,“七五”攻关的最终目的就是要钢球满足电机轴承配套的需要,从80年代的“七五”攻关至今,钢球的振动值水平又有新的提高,就振动值数值来说,已达到相当的水平,但不足的是数值的离散性一般都要在3dB以上,国外好的水平一般是2dB。随着无异音轴承的问世,对钢球的表面提出了更高的要求,不仅要解决缺陷球的漏网,更要解决钢球表面的各种伤痕,对全工作面的钢球来说,确实是项艰难的工作,日本采用光电外观的办法,但也不能彻底解决此问题,因为仪器检查有较好的稳定性,但灵敏度还是有限的。国内为解决此问题工艺上采用了各种办法,尽量防止和减少缺陷的漏检和伤痕的产生,当然光电外观检查也是一种不错的补救措施,目前国内也正在开展这方面的研究,期待早日可以用于生产。总之,国内钢球缺陷和表面伤痕的漏检比过去有很大提高,但还满足不了用户的要求。
钢球质量要赶上当代先进的实物质量水平,除了精度、粗糙度、表面质量、动态性能以外,可靠性和寿命是两项重要指标,国内钢球行业早在九十年代就开始做这方面的工作,当时为了军用、航空产品的可靠性,把涡流探伤技术成功地用于钢球制造,接着又把此技术扩展到汽车用钢球的制造,这一技术的成功,对钢球的可靠性起着至关重要的作用。由于我国深沟球轴承的大力发展,某种程度上,对噪音、异音比对可靠性寿命更注重,这是市场的导向,也许是价格的原因,在这种情况下,我国钢球在选材上和某些工艺环节上的差异,导致寿命(噪音寿命、疲劳寿命)差异较大,据统计,在70年代,国内轴承的损坏有70%是由钢球所致,近来有所下降,但钢球仍是轴承中最容易损坏的部分。随着我国汽车工业的大发展,汽车轴承的可靠性直接影响汽车的可靠性,因此轴承的可靠性和寿命必将放在重要地位,我们必须面对这一事实,去认真对待。钢球的噪音寿命不但需要钢球行业去研究,也需要轴承行业去研究,确切地说是需要双方共同研究,目标是降低轴承的噪音,提高轴承的寿命乃至疲劳寿命。从轴承钢钢球的质量现状看,进步不小,但发展仍不平衡,钢材优劣差异大,部分钢球质量已接近和达到国际先进水平,总体仍有差距,尚需我们继续努力。