钢球加工中烧伤的分析与控制(二)
钢球烧伤的原因及分析
2 烧伤原因及分析
2.1 机理分析
钢球在磨削加工时,其局部表面受到骤然磨削、挤压、摩擦等强力作用,导致局部温度瞬间上升过高,而后冷却形成钢球烧伤。当局部温度瞬间升高到高温回火温度时,又迅速冷却,产生的烧伤经冷酸洗后呈灰黑色,其组织为回火屈式体,这种烧伤被称为回火烧伤。回火烧伤伴有局部区域复杂的显微应力变化,因而会对钢球的质量(如寿命等)造成影响。当局部温度瞬间升高到淬火温度时,又迅速冷却,在该局部产生淬火现象,酸洗后呈灰白色的淬火马氏体,这种烧伤被称为淬火烧伤。淬火烧伤会造成钢球表面局部区域内显微组织和应力的较严重变化,破坏钢球表面组织和应力的均匀性,从而严重影响钢球的寿命。
2.2 工序分析
钢球加工中的光球、磨球和研球3个工序都可能产生钢球烧伤。经统计表明,这3个工序产生烧伤的几率分别占烧伤总数的17%,76%和7%。各工序发生烧伤几率的统计数据见表1。
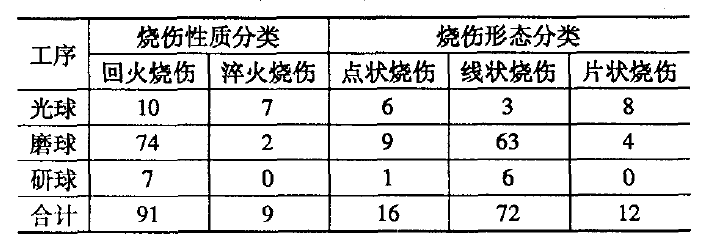
表1 各类烧伤产生的几率 %
由表1可以看出:
(1) 磨球工序是烧伤发生几率最高的工序,也是各钢球厂控制烧伤的关键工序。其中以线状回火烧伤为主,点状烧伤比例也较高,另有少量淬火烧伤。
(2) 光球工序由于压力大、速度快,产生烧伤比率也较高,特别是光球工序产生的淬火烧伤(如变色球),对钢球寿命影响最大(但当前被不少钢球厂所忽视)。
(3) 研球工序产生少量的点状、线状回火烧伤,由于已接近加工到成品而不好消除,同样存在影响钢球寿命的问题。
2.3 钢球规格分析
钢球加工实践中,不同规格钢球加工产生烧伤的几率有一定区别,通过统计分析表明,钢球越大,因其自转较差而产生烧伤的比例就越大。对Փ3.175 ~ 25.4 mm尺寸范围钢球产生烧伤(500批次)的统计结果为:Փ3.175 ~ 9525 mm钢球所产生的烧伤数约占9%;Փ10.0 ~ 14.288 mm钢球产生的烧伤数约占26%;Փ15.081 ~ 25.4 mm钢球烧伤数约占65%。
2.4 原因分析
点状、线状及片状烧伤产生的主要原因见表2。各类烧伤的直接原因不相同,但其间接原因有时也会混合,引起不同形状的烧伤。同时,加工过程中人为操作不当,也是产生各类烧伤的重要原因之一。
烧伤分类 | 直接原因 | 间接原因 |
线状烧伤 | 钢球自转不灵活而形成滑动摩擦 | 1. 砂轮板、铸铁盘的硬度过高; 2. 钢球的压力过小或铸铁盘、砂轮沟槽过深; 3. 加工钢球的沟槽深浅不一致,有的沟道对球的约束力不够,造成钢球连动或滑动; 4. 铸铁盘入口处喇叭口过于宽大,使钢球接触砂轮沟边沿; 5. 机床主轴精度、两磨板的平行度、沟槽的同心度未能满足要求; 6. 设备液压部稳定; 7. 铸铁盘或砂轮的沟槽不相吻合; 8. 同批钢球的批直径变动量大或混入大规格钢球; 9. 磨削液润滑性能过强,或混入机油等导致钢球连动或滑动。 |
点状烧伤 | 钢球受到硬质点挤压、撞击等 | 1. 铸铁盘、砂轮沟道有砂眼、硬质点、裂纹或掉粒(块)等; 2. 铸铁盘盘口有尖点或大毛刺; 3. 聚球刀板有尖点或大毛刺,或聚球刀板磨损而聚球不顺利; 4. 分配器与铸铁盘入口的交接处不吻合,或分配器后退使钢球在入口处短暂停留、窜沟,而被砂轮的沟沿打伤; 5. 设备转速太快或速度变化率太大,钢球突然加速运转 |
片状烧伤 | 钢球受到超强压力,只公转,不自转 | 1. 钢球在分配器和铸铁盘入口处进球不顺畅,在入口处堆积而堵沟,或者因其他原因造成某些沟槽太浅,当钢球重新进入该沟槽时产生片状、两极烧伤; 2. 换磨加工大规格钢球时,未做压沟处理; 3. 混入大规格钢球或机床上的死角球重新进入沟槽。 |